Ob defekte Kaffeemaschine, alter Rauchmelder oder ausrangiertes Smartphone: Die Mitgliedstaaten der EU müssen einen Teil ihrer elektronischen Altgeräte recyceln. Im Projekt ReconCycle hat ein internationales Forschungsteam seit 2020 nach Wegen gesucht, die komplexen Prozesse im Recycling vermehrt zu automatisieren. An dem von der EU geförderten Projekt ist Prof. Dr. Florentin Wörgötter vom Dritten Physikalischen Institut der Universität Göttingen beteiligt.
Herr Wörgötter, wie läuft bislang das Recycling von Elektroschrott ab und welche Herausforderungen gibt es?
Normalerweise werden die Geräte zunächst manuell zerlegt: Kabel werden entfernt, Batterien rausgenommen und manchmal noch weitere wertvolle Komponenten. Dann werden die Geräte in riesigen Anlagen zertrümmert und die Materialien physikochemisch getrennt. So entstehen große Fraktionen vorsortierter Komponenten, wie Metalle oder Plastik, die dann zu den Weiterverwertern transportiert werden. Diese Art der Trennung ist relativ unsauber, die Qualität des recycelten Materials also nicht so hoch wie gewünscht. Und die Arbeit ist sehr schmutzig, sehr laut und zum Teil gefährlich. Bei der Automatisierung geht es uns auch darum, die Arbeitsumgebung für das Personal zu verbessern.
Wo hat das Projekt ReconCycle bei der Vorsortierung und dem Umgang mit gefährlichen Stoffen angesetzt?
Bevor Elektrogeräte recycelt werden können, müssen alle Batterien herausgenommen werden, weil sie Brände auslösen können und weil sie giftig sind. Wir haben versucht, mit robotischen Maßnahmen Batterien aus Rauchmeldern und aus Geräten, die an Heizkörpern den Verbrauch messen, zu entfernen. Von solchen Geräten fallen Abertausende pro Jahr an. Die Rauchmelder sind oft vergossen, sodass die Arbeiterinnen und Arbeiter sie mühsam aufknacken müssen wie eine Nuss, um an die Batterien heranzukommen.
Da gibt es viele verschiedene Geräte und Gerätetypen, die in unterschiedlichem Zustand ankommen. Wie sind Sie vorgegangen, damit der Roboter sich zurechtfindet?
Schrott kommt tatsächlich in allen Farben und Formen an. Bevor man überhaupt einen Roboter einsetzen kann, muss man sicherstellen, dass die Maschine erkennt, was sie tun muss. Dafür kommen heutzutage Methoden des Machine Learning und Kameras zum Einsatz. Genau das ist unsere zentrale Aufgabe in Göttingen gewesen: die Zustands- und die Situationserkennung. Hat ein Roboter zum Beispiel ein Gerät geöffnet, sieht er ein neues Bild, aus dem er einen Schluss ziehen muss, was er als nächstes machen kann. Wir haben ein Kamerasystem entwickelt, das die Geräte erstmal klassifiziert. Ausgehend von bekannten Protokollen wird der Roboter zum Beispiel angewiesen, den Schraubenzieher anzusetzen und das Gerät aufzuhebeln. Dann prüfen wir mithilfe der Kamera, ob er das geschafft hat. Es ist also ein iterativer Prozess. Das zweite Ziel ist, dass die Maschine lernt, die Parameter zu verbessern für das nächste Mal. Unsere Projektpartner haben außerdem zusätzliche Hardware entwickelt, unter anderem eine automatische Schneidemaschine, die der Roboter zum Zerlegen nutzen kann.
Ihr Arbeitsfeld Computer Vision bedeutet also, dass Sie mit Ihrem Team programmieren und dann im Labor testen?
Zunächst ist es herkömmliche Programmierung. Wir zerlegen Bilder zum Beispiel in Kanten, in Ecken, in Farbflecke, in bestimmte Segmente. Daraus entsteht eine Struktur, aus der die Maschine einen Schluss zieht, zum Beispiel wo ist ein Loch, in das ich mit dem Schraubenzieher reingehen kann. Das mischen wir mit modernen KI-Methoden, sodass die Maschine charakteristische Elemente im Bild erkennt und anhand vieler verschiedener solcher Bilder lernt, Situationen besser zu verstehen. Auch wenn der Roboter eine Schraube in einem Gerät nicht klar erkennt, kann er lernen, wo mit großer Wahrscheinlichkeit eine Schraube sitzt.
Das Projekt endet im Juli dieses Jahres. Wie geht es weiter?
Erfreulicherweise hat unsere Forschung einen direkten industriellen Impact: Unser Projektpartner Elektrocycling in Goslar findet die von uns entwickelten Methoden so interessant, dass er sie bis zur Industriereife führen will. Unser Mitarbeiter Sebastian Herzog wird als Kleinunternehmer für die Firma in einem Projekt arbeiten, in dem bestimmte Metalle per Roboter aussortiert werden. Und wir stellen gerade einen Antrag für ein neues Forschungsprojekt, in dem es um das Recycling weicher Materialien geht. Die sind für Roboter schwierig zu handhaben.
Was sind das für Materialien?
Es soll um die drei Komponenten Kabel, Kleidung und Brennstoffzellen gehen. Die Mode ist so schnelllebig, dass die Kleidungsindustrie größere Produktionsmengen einfach wegwirft – weil es sehr aufwändig ist, die ganzen Knöpfe und Reißverschlüsse zu entfernen. Wenn wir diese Aufgabe automatisieren, könnte man den Stoff zumindest teilweise wiederverwerten. Die Brennstoffzellen enthalten extrem wertvolle Membranen mit viel Platin, aber auch mit sogenannten Ewigkeitsmaterialien, die in der Umwelt nicht abgebaut werden. Momentan werden die Membranen manuell mit Druck und Wasser abgelöst. Wir wollen sie automatisiert ablösen, indem wir sie vorsichtig auseinanderziehen.
Bleibt dafür das bisherige Forschungsteam bestehen?
Wir arbeiten schon lange mit unseren Kolleginnen und Kollegen aus Slowenien, Italien und Deutschland zusammen; auch im aktuellen Projekt hat es super funktioniert. Nun sollen noch weitere Personen hinzukommen. Die Option auf eine Weiterführung ist sehr erfreulich und wir profitieren von unserer bisherigen Arbeit. Wir wissen im Prinzip, wie wir die Erkennung von Altmaterialien und ihrer Komponenten durchführen können, und haben die Expertise, um Roboter bei der Hantierung anzuleiten.
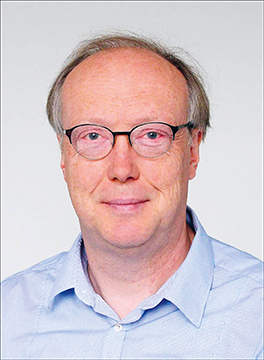